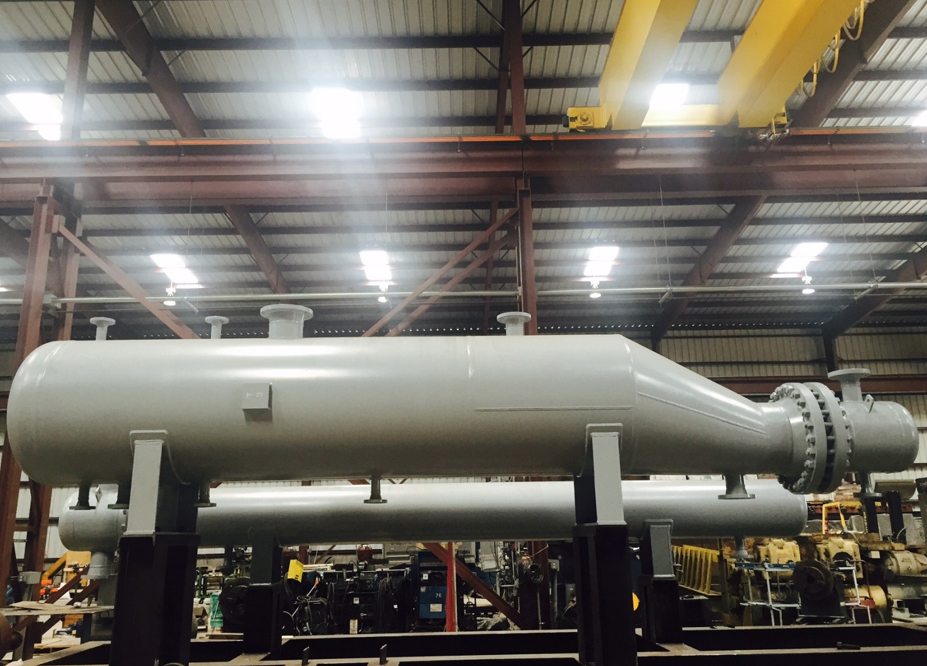
Shell and tube heat exchangers, like other types of heat exchangers, are one of the central and most costly components of most process units. SPS Systems manufactures shell-and-tube heat exchangers for the larger systems we manufacture and also for individual sale. Conforming to all TEMA B, C, and R standards for mechanical design, each SPS shell-and-tube heat exchanger is U stamped showing our commitment to ASME code standards. We also machine our own tubesheets and do our own thermal and mechanical design.
Shell-and-tube heat exchangers are a standard configuration used industry-wide. The hot side is isolated from the cold side by the use of a tubesheet and standard-sized tubing. There is a great deal of design flexibility whereby all types of process fluids in single- or multi-phased states can undergo heat transfer.
The thermal design of shell and tubes is a very sophisticated engineering discipline. SPS uses HTRI software for thermal design and in-house experience and the TEMA standards for mechanical design. SPS can build stainless and/or carbon steel shells with stainless, carbon steel, cupro-nickel, or copper tubes. Most of the configurations are BEM, BEU, AKU, or BKU.
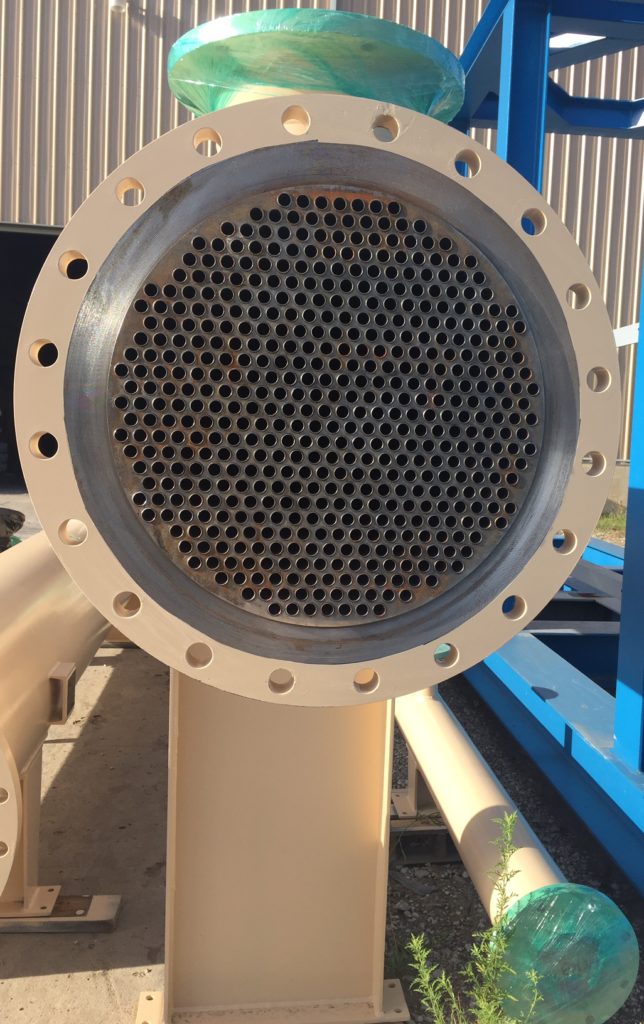
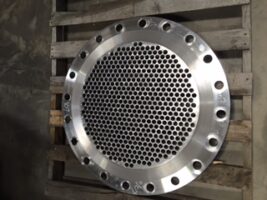
Advantages of SPS Heat Exchangers
- We can do a complete process design, optimizing pressure drop with heat transfer coefficient
- We machine our own tubesheets and baffles and can provide quick turnaround on the design and fabrication of heat exchangers as required
- We can re-tube and recondition existing heat exchangers
- We will re-rate your current in-place heat exchanger and offer suggestions on modifications to optimize exchanger performance
- Our process engineers can come to your plant to assess process parameters and suggest modifications as necessary
Another common application for heat exchanger engineering involves cooling air. For more information about SPS Air Coolers, click here.
For more information about SPS Shell and Tube Heat Exchangers or any other SPS product, contact us.
Certifications
SPS Systems, Inc. maintains certification with the American Society of Mechanical Engineers (ASME) for “U” stamped vessels and the National Board for “R” stamped repairs.